Data
Background
Thermal management is a significant challenge for new-generation turbofan aero-engines, and one critical component in this system is the Air-Cooled Oil Cooler (ACOC). The primary function of the oil cooler is to reduce the oil's temperature by extracting heat with the help of bypass ram-air, ensuring that the engine operates within optimal temperature ranges. In some aircraft, ACOCs are used alongside Fuel-Cooled Oil Coolers (FCOCs) to enhance cooling efficiency. Traditionally, these heat exchangers are manufactured using conventional methods like brazing, which require multiple steps to complete the final product.
This approach limits performance capabilities and results in bulky products. Additionally, oil coolers made with these methods incur substantial tooling costs for each design change and demand long-term contractual commitments from aerospace OEMs. These limitations present challenges to the aerospace industry, which is under increasing pressure to reduce lead times, improve engine thermal efficiency, and meet stringent carbon footprint regulations. One effective way to enhance aircraft energy efficiency is by reducing mass. To address these challenges, a novel approach is necessary
The challenge
The primary challenge for us was to design an ultra-efficient and lightweight oil cooler that could be integrated into the aircraft's thermal management system. The oil cooler needed to meet the following requirements:
- Lightweight Design: Achieve a weight reduction of 30% or more compared to the current benchmark without compromising performance.
- High Thermal Efficiency: Ensure optimal performance in various environmental conditions (take-off, cruise).
- Compact Size & integrable: Fit within the existing space constraints and system interfaces.
- Structural integrity: The oil cooler must sustain a proof and burst pressure of 6 and 12 Bar, and meet standard test requirements
Approach
Our team has developed an end-to-end digital streamlined solution for the ACOC using our innovative design approach and state of the art powder bed fusion process.
1. Digitization and Automation of the Oil Cooler Value Chain
- Streamlining activities from the requirement definition phase to final inspection and delivery.
- Reducing design iteration lead time through single-part, single-step manufacturing, eliminating multi-step activities in traditional supply chains.
- Facilitating design iterations and upgrades by digitizing design and manufacturing processes.
- Eliminating inventory, logistics, and tooling costs with local additive manufacturing (AM) production.
2. Reduction of Heat Exchanger Weight and Validation
- Utilizing a library of novel and complex heat transfer surfaces achievable only through AM and our proprietary thermal design optimization tools.
- Employing advanced numerical simulation tools (CFD, FEA) for accurate predictions of thermal and pressure performance.
- Optimizing process parameters for thin, leak-free walls and fine features.
- Integrating multiple parts/functions into a single component.
- Testing and validation
3. Cost Reduction and Production Strategies for Competitive Aerospace Heat Exchanger Products
- Automating manufacturing file generation to create nearly off-the-shelf products that meet ACOC requirements.
- Aligning design and manufacturing activities to produce features suitable for AM processing and post-processing.
- Enhancing process repeatability by establishing geometric limits and tolerances for consistent AM process builds.
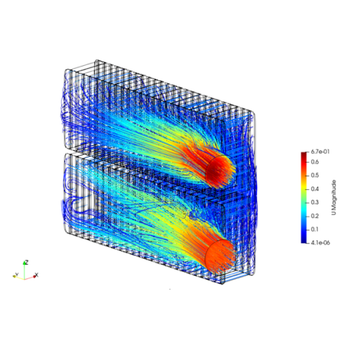
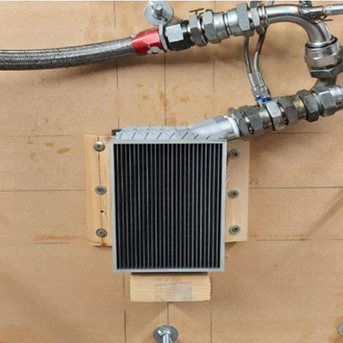
In order to validate the heat exchanger performance, a series of CFD studies were performed across a range of designs and conditions. This had the objective to assure a uniform distribution across the heat exchanger core as well as support the pressure loses predictions from the analytical models. Experimental validation is also a key part of the process to validate the predicted performance of the heat exchanger.
The outcome
The implementation of the new heat exchanger design approach led to significant improvements:
- Weight Reduction: An oil cooler that is 57% lighter and more compact than its conventional counterpart.
- Design flexibility: The design is flexible and can be customized for each system requirement and design changes.
- Shorter lead time: The delivery lead time is significantly reduced through design and analysis automation.
- Lower drag: The aircraft drag is reduced through low air pressure drop, resulting in improved fuel efficiency and reduced emissions.
- Competitive cost: The design and AM process is optimized to achieve a competitive cost for the aerospace industry.
Conclusion
This ACOC case study demonstrated the transformative impact of innovative thermal management solutions in the aerospace industry. By integrating advanced design techniques and additive manufacturing, we exceeded our initial weight reduction targets, accelerating the industry goals of enhancing efficiency and sustainability.
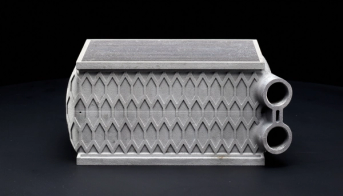
Contact Us
To explore how our heat exchanger technology can elevate your next project, contact us