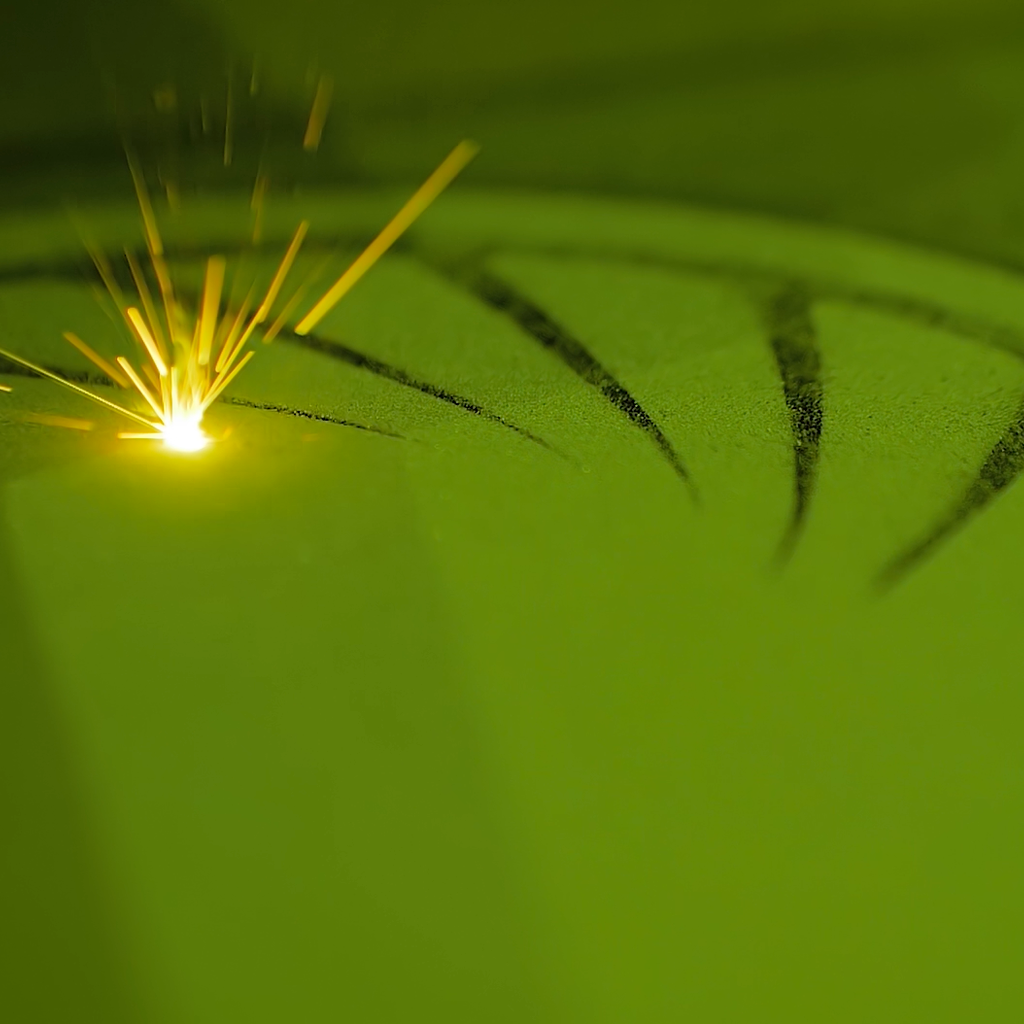
Additive Manufacturing Technology
Pushing the boundaries of thermal design with Additive Manufacturing
By using a multi-laser, powder bed fusion of metal, we create one-piece heat exchangers that are far more intricate than traditional engineering can achieve.
Additive Manufacturing offers several advantages compared to traditional manufacturing methods. Here are some key benefits:
Available range of Materials
Additive Manufacturing can process a wide range of metallic materials that can be used for our thermal solutions. Additionally, we can accommodate applications requiring specific material development. This versatility in material selection allows for the customisation of heat exchangers to meet exact thermal and mechanical specifications.
Enhanced heat transfer
Additive manufacturing allows for the creation of complex and intricate geometries that would be challenging or impossible with traditional methods. This flexibility in design can enhance the efficiency of heat exchangers by optimising their shape and surface area.
The ability to design and manufacture complex lattice structures enables the production of lightweight heat exchangers. This is particularly advantageous in aerospace and automotive applications where weight reduction is a critical factor for fuel efficiency and overall performance.
Design Iteration
Additive manufacturing allows engineers to quickly iterate designs and test different configurations. This accelerates the product development cycle and facilitates the optimization of heat exchanger performance. This is particularly important during system development and innovation.
Customization
Additive manufacturing enables the production of highly customised heat exchangers to meet your specific requirement. This is beneficial in applications where standard, off-the-shelf solutions may not be bulky or unfeasible.
Conformal shape an optimal system integration
The design flexibility of AM architecture allows for seamless integration with any system. This means your design envelope defines the heat exchanger, not the other way around. Our heat exchangers are highly adaptable to your specific interface requirements.
Reduced Lead Time
Additive manufacturing can significantly reduce lead times for producing heat exchangers. The ability to directly convert digital designs into physical objects without tooling streamlines the manufacturing process, leading to faster production.
On-Demand Production
Additive manufacturing supports on-demand and localised production. This is advantageous for producing heat exchangers tailored to specific needs without the need for large inventories or long supply chains.
Sustainable manufacturing
Traditional manufacturing processes often involve subtractive methods, where excess material is removed to create the final product. In contrast, additive manufacturing builds components layer by layer, minimising material waste and enhancing manufacturing sustainability. Additionally, it supports decarbonization in the operational stage of many systems by enabling more efficient energy or fuel consumption during operation.