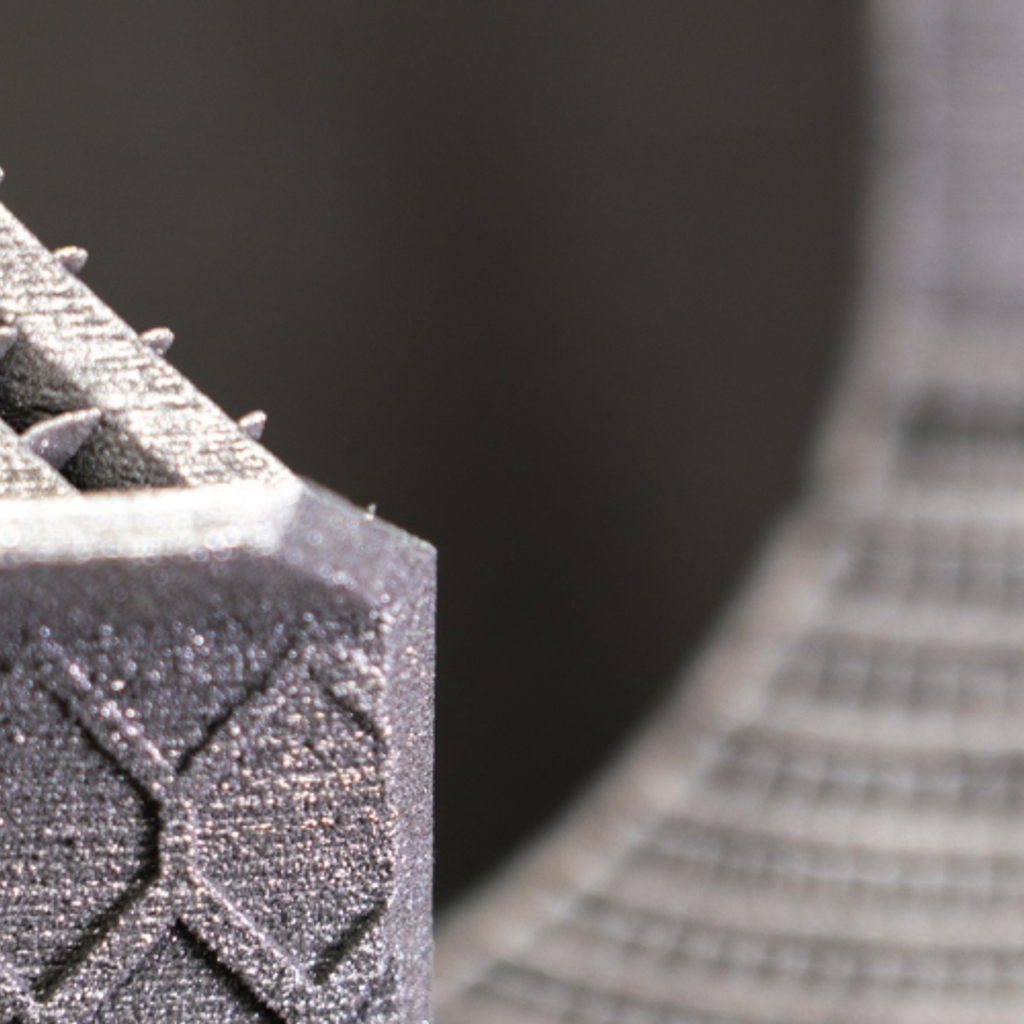
Heat Exchanger Technology
Heat exchangers should serve your system, not define it
Morpheus Designs is leading the advancement of ultra-efficient and compact heat exchangers, utilising Additive Manufacturing (AM) and proprietary heat transfer geometries and design optimization tools.
Our team has developed an in-house method of rapidly creating heat exchangers. This method is based on a decade of expertise in designing and manufacturing AM heat exchangers. An end-to-end digital process, it provides several advantages:
Design automation and Digitalisation
We don’t pivot between 1D, CAD software and analysis. Instead, we streamline heat exchanger design, analysis, and manufacturing with automation and digitalisation, significantly cutting lead times and costs. Automated processes, from 1D sizing to final manufacturing file generation, reduce design iteration time, promoting flexibility and eliminating multi-step activities in traditional supply chains.
We can select from a library of validated heat transfer and core architectures – speeding the process of finding the right design for your use case.
Unmatched Weight and Volume Reduction
We achieve significant size and weight reductions compared to the competition by utilising a repository of optimised heat transfer geometries, enabled by extensive Computational Fluid Dynamics (CFD), structural optimization using FEA, and experimental validation. With a deep understanding of AM process limitations across various materials, we continuously optimise quality and feature definition, focusing on creating airtight, leak-free complex thin walls.
By employing a multi-laser system & optimal scanning strategy, we can achieve a substantial increase in the part productivity. Our innovative manifold designs in multipart integration ensure uniform flow distribution and seamless integration with various system components.
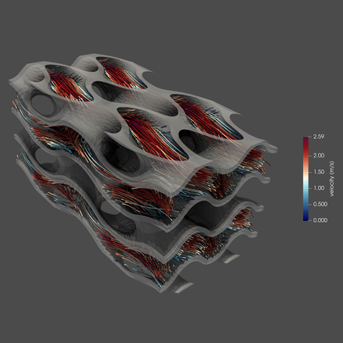
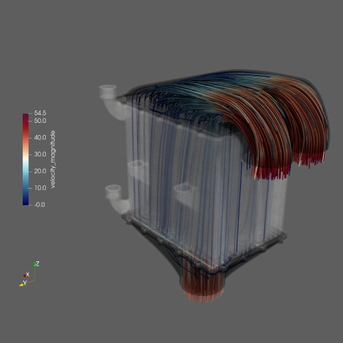
Streamlined test and validation method
Testing and validation of heat exchangers are critical steps to verify their performance against predictions and ensure compliance with customer requirements. We simulate (CFD, FEA) and test heat transfer & pressure drop, proof pressure, burst pressure, vibration, corrosion, fouling, thermal shock, and more depending on requirement and in compliance to industry standards. All our heat exchanger products also go through extensive physical testing before delivery.
The test data is cross checked against FEA and CFD results to identify and address any disparities.
We collaborate with partners to get comprehensive mechanical data at both as-built and heat-treated stages. This typically involves tests at room temperature as well as elevated temperatures.
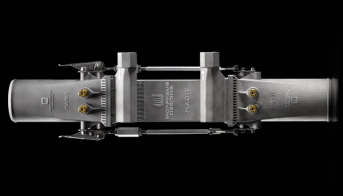