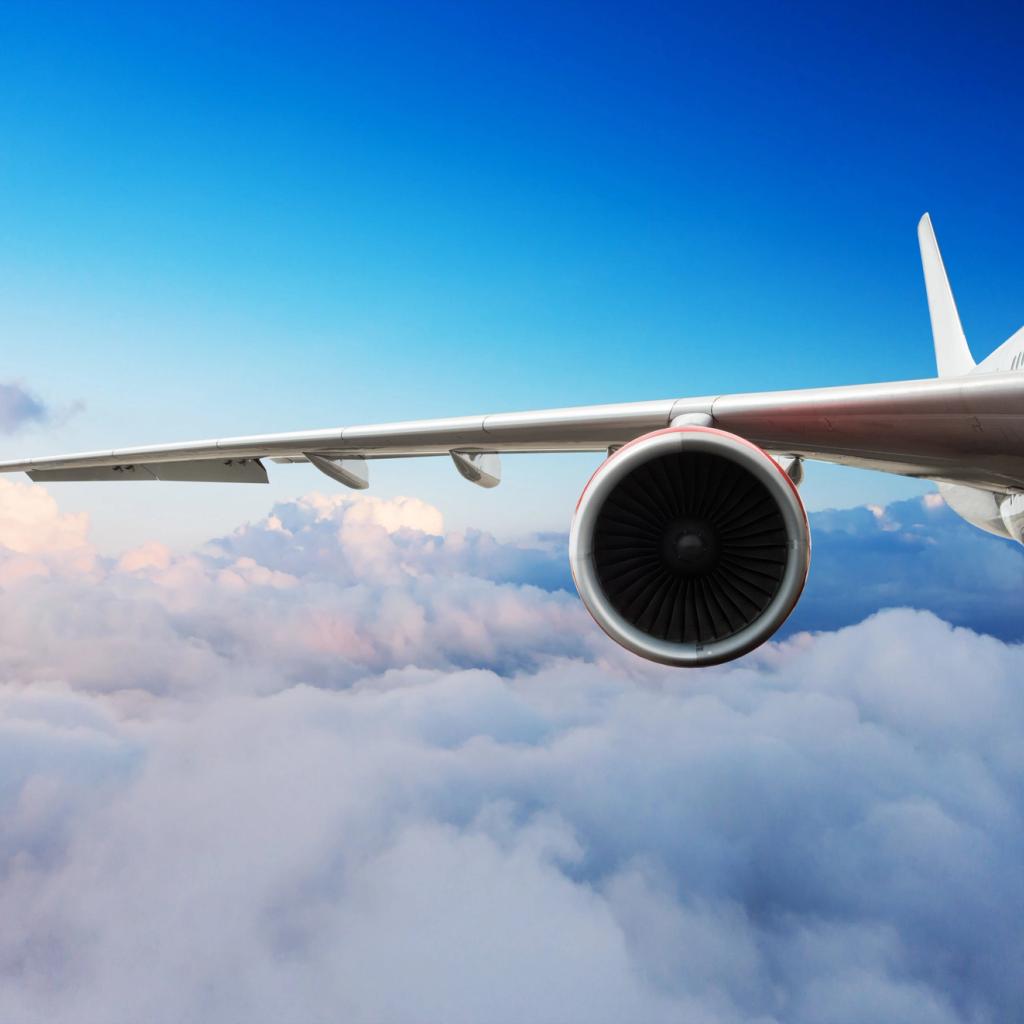
Aerospace
Innovative cooling solutions for Net-Zero Flight
Aerospace applications utilise a diverse range of heat exchangers with variations in function and construction. These include air-to-air, air-to-liquid, liquid-to-liquid, and two-phase heat exchangers, each serving specific purposes in managing heat within aircraft systems.
Designing aerospace heat exchangers requires careful consideration of thermal performance, weight, vibration resistance, congealing capability, pressure requirements, and high reliability, all of which are critical factors.
Additive manufacturing has been increasingly used to make functional parts for the new generation of aircraft. We’re pushing the technology further, making previously impossible thermal solutions for the aerospace market.
Here some revolutionary heat exchangers developed for aerospace applications.
Fuel cell heat exchangers
The next-generation hydrogen-powered aircraft aim to reduce carbon emissions and fossil fuel dependency, aligning with global sustainability efforts. A significant effort has been focused by main industry players on fuel cell technologies. Morpheus Designs is at the frontier of new cooling solutions for the hydrogen fuel cell propulsion.
Our liquid cooling heat exchangers manage fuel cell temperature by circulating coolant through channels or plates in direct contact with the fuel cell stack. This process prevents overheating, ensuring optimal efficiency and reliability. A more effective way of cooling is through two-phase heat transfer. Two-phase cooling transitions a working fluid between liquid and vapour phases, offering superior heat transfer and enhancing fuel cell performance, temperature uniformity, particularly in high-power-density systems.
A major advancement in our thermal solutions is our innovative condenser, essential for condensing evaporated liquid in a closed-loop cooling system. Our analysis shows that the mass and dimensions can be reduced by up to 60% compared to traditional designs. This significant reduction is achieved through the use of multi-laser Additive Manufacturing (AM) and improved film condensation designs developed by Morpheus Designs, resulting in ultra-compact condenser units specifically tailored for the fuel cell market.
Morpheus single-phase and two-phase cooling solutions are both designed to the highest aerospace standards.
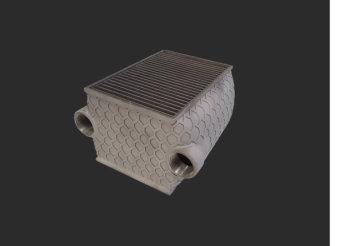
Precoolers
Precoolers disposed within a nacelle are used as the first stage of cooling the bleed air. The precooler's primary function is to initially reduce the temperature of the bleed air taken from the aircraft engine before it is routed to other systems.
Our precoolers are optimised for high thermal performance, weight, and reliability.
Functions:
Reduce the temperature of the bleed air
Bleed air heat exchangers
The bleed air heat exchanger further cools the already precooled bleed air to the required temperature for specific uses within the aircraft systems, such as the environmental control system (ECS), avionics cooling, and cabin pressurisation. They are vital to the operational performance of the aircraft.
Our bleed air heat exchangers are constructed from materials such as 316 stainless steel and Inconel 625 to withstand high-temperature inlet conditions.
Functions:
Cools high temperature engine bleed air using ram-air, which is ambient air collected during flight.
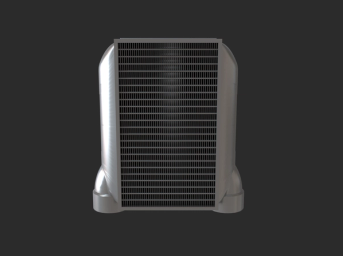
Air Cooled Oil Coolers (ACOC)
Air-cooled oil coolers (ACOC) are vital components in aircraft systems, playing a crucial role in dissipating heat from the engine oil. The cooling ram-air is either drawn in naturally by the airflow during flight or directed specifically to the cooler through bypass ducting. ACOCs are essential for managing engine temperature, promoting optimal performance, and ensuring the longevity of aircraft engines.
We provide custom-designed Aluminum ACOCs tailored to meet various heat duty and pressure requirements, with the option to include integrated de-congealing and bypass valves.
Functions:
Cools high temperature engine oil using ram-air.
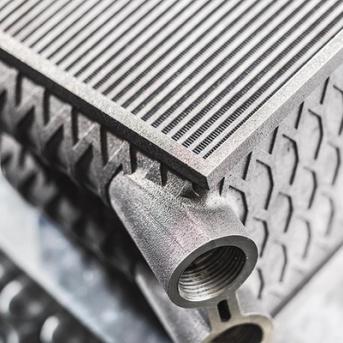
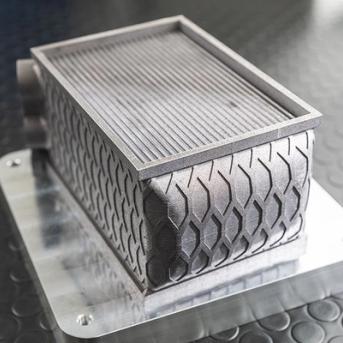
Fuel-Cooled Oil Coolers (FCOC)
Fuel-cooled oil coolers are specialised heat exchangers that utilise aircraft fuel as a cooling medium to cool engine oil or hydraulic fluid. By extracting heat from the engine oil before recirculating it for lubrication, these coolers play a critical role in maintaining optimal oil temperature for efficient lubrication and heat dissipation in aircraft engines. This method of cooling contributes to overall thermal management and resource utilisation efficiency during flight.
Functions:
Cools engine oil using jet Fuel.
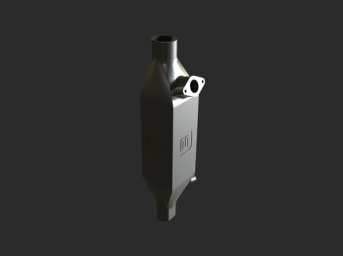
Evaporators & Condensers
Evaporators and condensers are vital components in aircraft environmental control systems. Evaporators cool and dehumidify cabin air by evaporating refrigerant to absorb heat and moisture. Condensers then release this heat to the outside air, completing the refrigeration cycle and maintaining optimal cabin conditions for passenger comfort and safety during flight.
Functions:
Utilised within the Environmental Control System (ECS) to regulate temperature
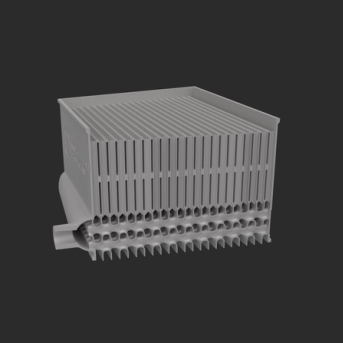
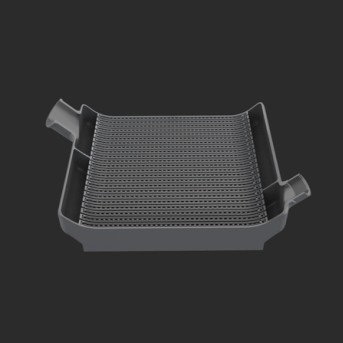