Data
Background
Traditionally, recuperators used in microturbine systems have been manufactured using conventional diffusion bonding techniques. While effective, these methods often result in bulky designs and complex assembly processes, limiting both packaging efficiency and overall system performance.
To address these challenges, we developed an additively manufactured recuperator that offers a more compact and efficient solution. The goal was to significantly reduce the package envelope, cost, and improve the overall efficiency of the microturbine system.
Challenges
Large Space Requirements
Traditional recuperators are typically designed in a box-style configuration, which requires a significant amount of space. This bulky design limits flexibility in microturbine systems, where compactness is critical for optimal performance. Additionally, the long ducting required to connect the recuperator to other components increases the system's footprint and adds complexity to the overall design.
Parasitic Losses
- Heat Loss: The long ducts used in traditional designs often experience significant heat loss due to the high temperature differential between the hot gases inside the recuperator and the cooler ambient environment. Without proper insulation, this leads to parasitic thermal losses, reducing overall system efficiency.
- Pressure Drop: The extended ducting paths and internal flow restrictions of conventional recuperators result in pressure drops. This forces the system to expend more energy pushing the working fluid through the recuperator, leading to further efficiency losses and increased operational costs.
Material Limitations
Traditional manufacturing methods impose material limitations that restrict the temperature capabilities of recuperators. While high-temperature materials are desirable to enhance efficiency, traditional manufacturing processes often lead to compromises in material selection. This inability to push high-temperature boundaries results in suboptimal thermal performance.
Thermal Stresses and Structural Failure
Poor design in traditional recuperators can lead to uneven thermal distribution, causing significant thermal stresses during operation. These stresses arise when different parts of the recuperator experience varying temperatures, resulting in expansion and contraction at different rates. Over time, this mismatch creates mechanical strain, which can lead to:
- Cracking in critical areas, particularly at welds or joints.
- Fatigue failure in areas subjected to repetitive heating and cooling cycles.
- Leakages caused by distortion of ducting or failure at high-stress points.
These thermal stresses, if not properly addressed in the design phase, significantly increase the risk of recuperator failure, leading to costly repairs, downtime, and reduced system reliability.
Complexity of Insulation
In traditional designs, ducting and recuperator surfaces often need to be insulated to minimize heat loss. However, insulating components at high temperatures presents additional challenges:
- Material degradation over time is due to constant exposure to high temperatures and thermal cycling.
- Increased weight and volume from insulation, which further affects the compactness of the system.
Some of these challenges stem from manufacturing limitations and the multi-step processes required to produce the finished part.
Our Innovative Approach
A key focus of our design approach to address the above challenges was to create a compact recuperator with integration potential for MGT components while remaining cost-competitive through reduced build times. We developed an annular recuperator and collaborated with Renishaw to manufacture it using their cutting-edge TEMPUS technology on the RenAM 500 series of metal powder bed fusion (PBF) systems. TEMPUS, a revolutionary scanning algorithm developed by Renishaw, significantly boosts productivity without compromising part quality. By enabling the laser to fire simultaneously with the recoater movement, TEMPUS can reduce build times by up to 50%, depending on the part's geometry.
The outcome
In this specific case study, the use of TEMPUS technology resulted in a 38% reduction in build time compared to a standard process setting without TEMPUS. The integrated design of the recuperator also contributed to enhanced system performance by:
- Reducing the package envelope of the recuperator, making the microturbine system more compact.
- Increasing efficiency by optimizing heat transfer, thereby improving the overall energy output of the system.
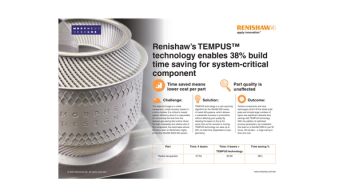
Conclusion
The work has demonstrated a significant reduction in both build time and size. The next step is to manufacture the part using a high-temperature nickel alloy and conduct full thermal and pressure performance testing.
Contact us
To explore how our innovative recuperator technology can help your project, contact us