Datos
Antecedentes
Tradicionalmente, los recuperadores utilizados en sistemas de microturbinas se han fabricado mediante técnicas convencionales de soldadura por difusión. Aunque son efectivas, estos métodos a menudo resultan en diseños voluminosos y procesos de ensamblaje complejos, limitando tanto la eficiencia del empaquetado como el rendimiento general del sistema.
Para abordar estos desafíos, desarrollamos un recuperador fabricado aditivamente que ofrece una solución más compacta y eficiente. El objetivo era reducir significativamente el tamaño del paquete, el costo y mejorar la eficiencia general del sistema de microturbinas.
Desafíos
Grandes Requisitos de Espacio
Los recuperadores tradicionales generalmente están diseñados con una configuración en forma de caja, lo que requiere una cantidad significativa de espacio. Este diseño voluminoso limita la flexibilidad en los sistemas de microturbinas, donde la compacidad es crítica para un rendimiento óptimo. Además, la larga canalización necesaria para conectar el recuperador con otros componentes aumenta la huella del sistema y añade complejidad al diseño general.
Pérdidas Parasitarias
- Pérdida de Calor: Los largos conductos utilizados en diseños tradicionales a menudo experimentan una pérdida de calor significativa debido a la gran diferencia de temperatura entre los gases calientes dentro del recuperador y el ambiente más frío. Sin el aislamiento adecuado, esto conduce a pérdidas térmicas parasitarias, reduciendo la eficiencia general del sistema.
- Caída de Presión: Las trayectorias extendidas de los conductos y las restricciones internas de flujo de los recuperadores convencionales resultan en caídas de presión. Esto obliga al sistema a gastar más energía empujando el fluido de trabajo a través del recuperador, lo que conduce a mayores pérdidas de eficiencia y un incremento en los costos operativos.
Limitaciones de Material
Los métodos tradicionales de fabricación imponen limitaciones de material que restringen las capacidades de temperatura de los recuperadores. Aunque los materiales de alta temperatura son deseables para mejorar la eficiencia, los procesos de fabricación tradicionales a menudo conducen a compromisos en la selección de materiales. Esta incapacidad para ampliar los límites de temperatura alta resulta en un rendimiento térmico subóptimo.
Tensiones térmicas y fallo estructural
Un diseño deficiente en los recuperadores tradicionales puede llevar a una distribución térmica desigual, causando tensiones térmicas significativas durante la operación. Estas tensiones surgen cuando diferentes partes del recuperador experimentan variaciones de temperatura, resultando en expansión y contracción a distintas velocidades. Con el tiempo, esta discrepancia crea una tensión mecánica, que puede conducir a:
- Grietas en áreas críticas, especialmente en soldaduras o uniones.
- Fallo por fatiga en áreas sometidas a ciclos repetitivos de calentamiento y enfriamiento.
- Fugas causadas por la deformación de los conductos o fallos en puntos de alta tensión.
Estas tensiones térmicas, si no se abordan adecuadamente en la fase de diseño, aumentan significativamente el riesgo de fallo del recuperador, lo que conduce a reparaciones costosas, tiempo de inactividad y reducción de la fiabilidad del sistema.
Complejidad del aislamiento
En diseños tradicionales, los conductos y las superficies del recuperador a menudo necesitan ser aislados para minimizar la pérdida de calor. Sin embargo, aislar componentes a altas temperaturas presenta desafíos adicionales:
- La degradación del material a lo largo del tiempo se debe a la exposición constante a altas temperaturas y al ciclo térmico.
- Aumento del peso y volumen por el aislamiento, lo que afecta aún más la compacidad del sistema.
Algunos de estos desafíos provienen de las limitaciones de fabricación y los procesos de múltiples etapas necesarios para producir la pieza terminada.
Nuestro Enfoque Innovador
Un enfoque clave de nuestro método de diseño para abordar los desafíos mencionados fue crear un recuperador compacto con potencial de integración para componentes de turbinas de gas micro (MGT) manteniendo la competitividad en costos a través de la reducción de los tiempos de construcción. Desarrollamos un recuperador anular y colaboramos con Renishaw para fabricarlo utilizando su avanzada tecnología TEMPUS en la serie RenAM 500 de sistemas de fusión de lecho de polvo metálico (PBF). TEMPUS, un algoritmo de escaneo revolucionario desarrollado por Renishaw, aumenta significativamente la productividad sin comprometer la calidad de la pieza. Al permitir que el láser se dispare simultáneamente con el movimiento del recubridor, TEMPUS puede reducir los tiempos de construcción hasta en un 50%, dependiendo de la geometría de la pieza.
El resultado
En este caso de estudio específico, el uso de la tecnología TEMPUS resultó en una reducción del 38% en el tiempo de construcción en comparación con una configuración de proceso estándar sin TEMPUS. El diseño integrado del recuperador también contribuyó a mejorar el rendimiento del sistema mediante:
- Reduciendo el tamaño del envoltorio del recuperador, haciendo el sistema de microturbina más compacto.
- Aumentando la eficiencia mediante la optimización de la transferencia de calor, mejorando así la producción energética total del sistema.
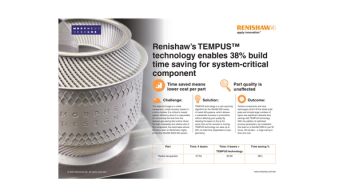
Conclusión
El trabajo ha demostrado una reducción significativa tanto en el tiempo de construcción como en el tamaño. El siguiente paso es fabricar la pieza utilizando una aleación de níquel de alta temperatura y realizar pruebas completas de rendimiento térmico y de presión.
Contáctenos
Para explorar cómo nuestra innovadora tecnología de recuperador puede ayudar a su proyecto, contáctenos …